October 25, 2021
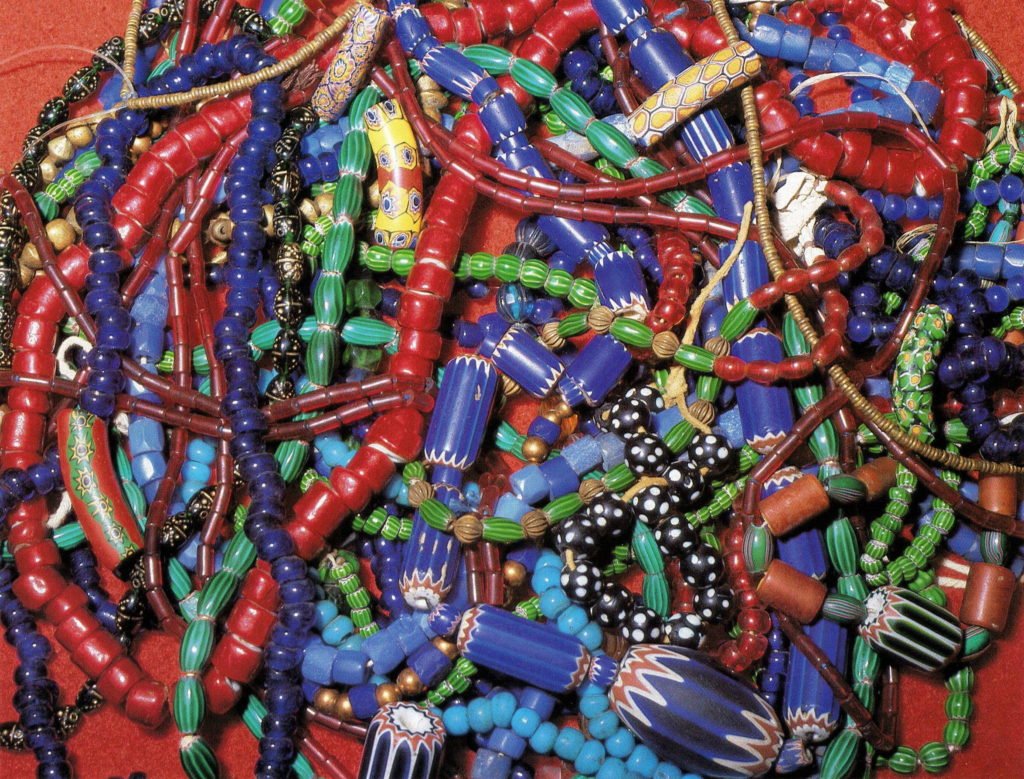
This story was originally published by St. Stephens Indian Mission Foundation in VOL. XVI JUL/AUG/SEPT 1986 NO. 3. St. Stephens Indian Mission Foundation owns the copyright, and the story is reprinted here with permission from the Foundation. More information on the Foundation can be found following the story or by clicking on the link above.
The story of glass beads began centuries before the Indians of North America used them for decoration and trade. One of the earliest production of glass beads has been traced to the Ancient Egyptians. Remains of a thriving glass works industry, dating back to 1365 B.C., has been discovered in Egypt. Much of the early history of beads is, and may remain, a mystery. The secrets of glass making were guarded by the glass bead industry itself. These secrets were so confidential that an early glass maker did not dare move to another country and establish his own business. Should the glass maker divulge any of the industry’s secrets, his life and the lives of his family would be in great danger.
Another part of this mystery is due to the fact that much of the early glass making was done in what are now Soviet-held countries. Very little of the historic glass making techniques of these countries have been made accessible to the rest of the world. As archaeologists continue to study materials found at various sites throughout the world, this mystery may be closer to being solved.
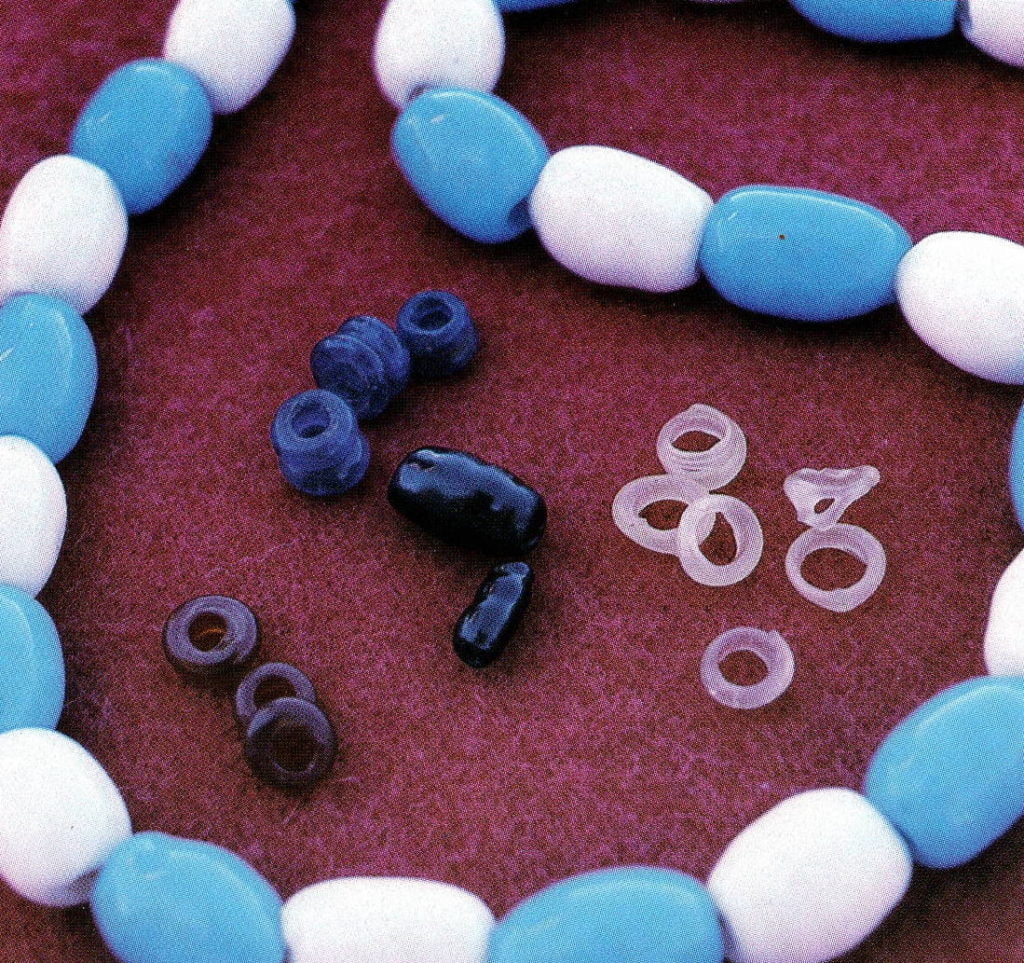
Although glass factories were started in Lebanon several thousand years ago, and are still in production today, the Italian city of Venice is known as, “The Mother of Modern Beads.” It is known that in 1224 A.D., a guild of Venetian glass makers existed and that in 1291, a large portion of their industry was moved to the Island of Murano — located just north of Venice. The move was made to prevent the possibility of a fire, should an accident occur with the furnaces used by the glass industry. It was feared that a fire would not only destroy the factory, but also the city of Venice.
For some two hundred years, beads were made in Murano by a method known as “winding.” With this method, beads were made individually by drawing a molten glob of glass out of the furnace and winding it around an iron rod until a desired size was obtained. Glass of another color could then be added or the bead could be decorated with a design. Glass itself is not naturally colored so agents were added to molten glass: cobalt made blue; copper produced green; tin made a milky white; and gold resulted in red. Early samples of wound beads are sometimes found to be quite simple and crude. Wound beads that have been done by a master glass maker are so perfect, that it’s hard to find a seam where the glass merged together.
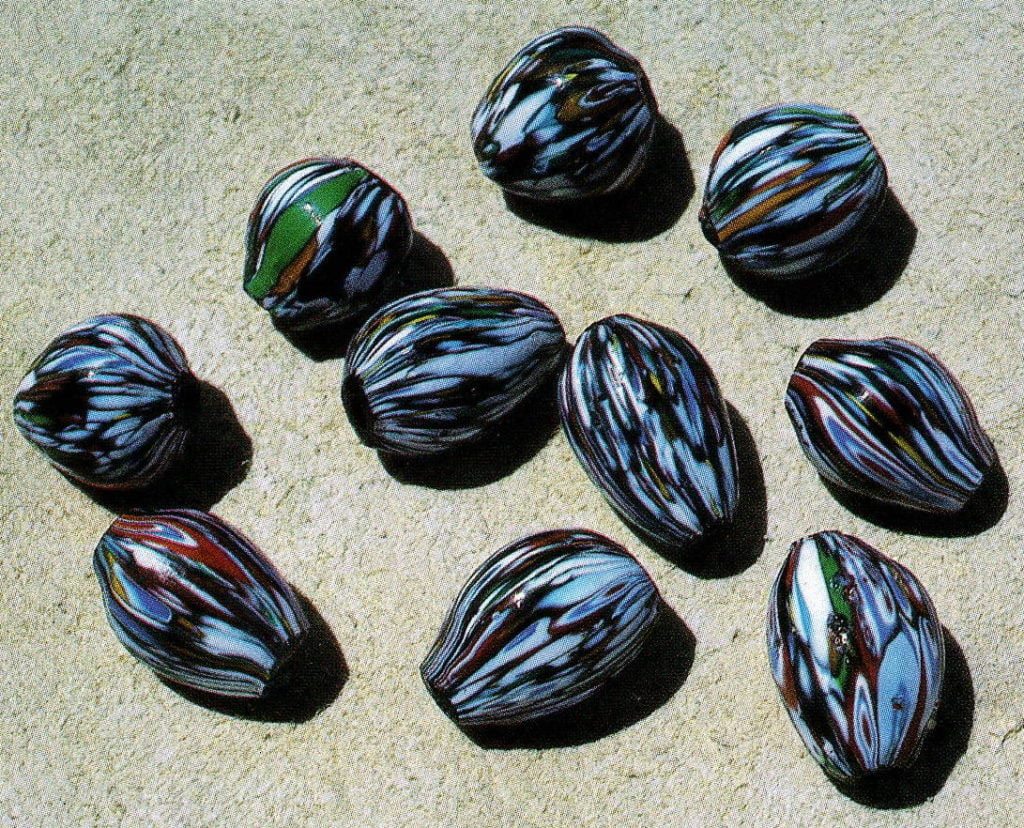
Other techniques of bead making were also used. Glass was sometimes pressed to leave a distinguishable seam where the molds came together. Another method was to “blow” glass beads. In using this method, a glob of molten glass was removed from the furnace and the desired shape of the bead was obtained by breathing through a glass tube — much the same way that glass vases or cups are made.
The industry and the world moved along at a rather reserved pace until the early 1400’s, when the Age of Exploration dawned. European countries were sending explorers to unknown parts of the world to discover and conquer new land. Venetian beads were taken along on nearly all of these expeditions, creating an influx of new customers for the glass makers. Explorers carried with them glass, porcelain, and/or metal beads to be used as gifts or for trade. This gave the bead industry a trans-world status. The slow method of winding beads could not keep up with this new demand.
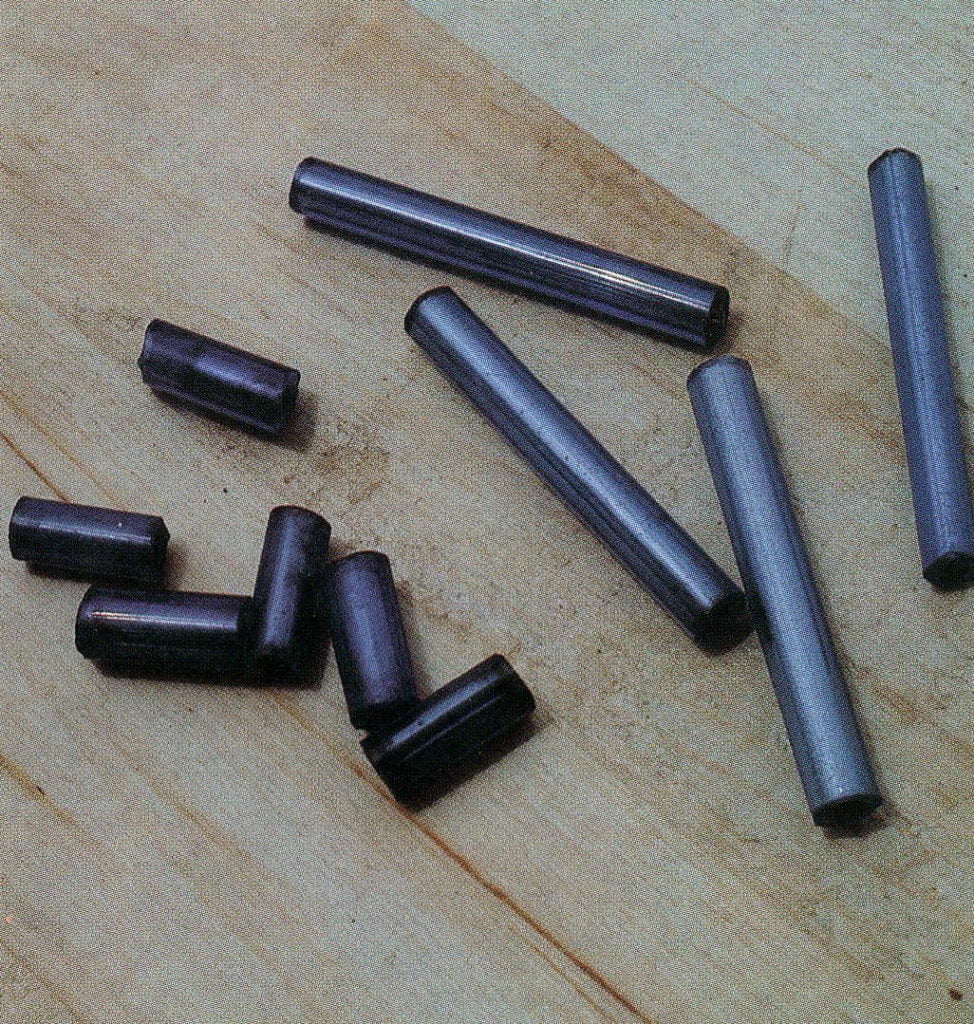
Around 1490, it is believed that Venetian bead makers re-invented the art of “drawing” beads. Re-invented, because the early Egyptians might well have used this process centuries before. This procedure requires a master glass maker to take a glob of molten glass from the furnace and form a cylinder. He would then work this cylinder into a desired shape and possibly add other layers of glass. After the master glass maker attached a rod to the opposite end of the cylinder, his assistant would take the rod and run with it down a long corridor before the glass had a chance to cool. The resulting tube was usually about one hundred and twenty meters long. The length of the tube and the amount of glass used determined the size of beads. After the tubes cooled, they were cut into lengths of about a meter long and then cut into beads of various sizes. The beads were then placed in a large metal drum with a mixture of lime, carbonate, sand, carbon and water. While the metal drum turned, heat was carefully applied to the outside causing the rough-cut edges on the beads to be smoothed. After removing the beads from the drum they were cleaned to keep any further abrasion from occurring. The beads were placed in a sack of fermented bran and shaken vigorously. This procedure polished the beads which were then ready to be strung according to size, shape and color.
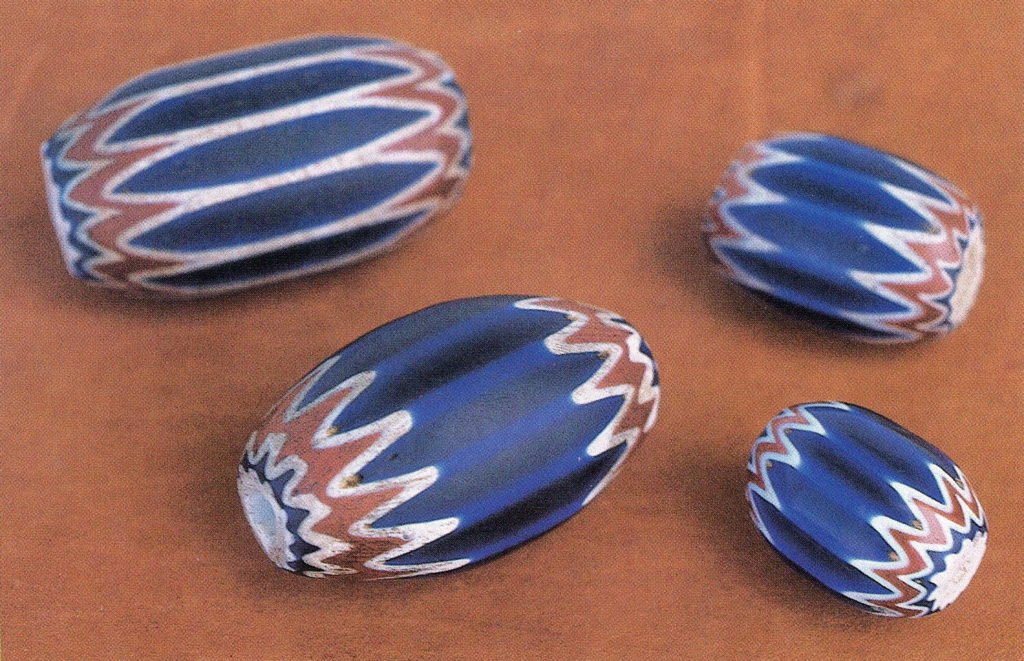
Drawn beads of Venice are divided into two distinct types: “Paternoster,” which were originally used as large beads on a rosary; and “Magaritierie” (Latin for pearl or bead), this smaller bead is also known as the “Pound” bead because they were sold by weight. The monochrome beads of today are not much different from those made five hundred years ago, using the same method.
The aristocrates of Venetian beads are the “Chevrons” or “Rosettas,” also known as the “Star” beads. These Paternoster beads are multi-layered and corrugated to produce a star-pattern on the ends and often result in stripes on the outside. Because this bead was hand-faceted to reveal the characteristic star-pattern, it was difficult to make. The original Chevron bead had seven layers, but around 1580, in order to meet the demand for this bead, variations with only four layers were made. These beads were tumbled instead of being hand-faceted to speed-up the process. The Chevron has become a popular bead the world over, the most common being the blue, red and white combination. Chevrons that are green and white or red and white are not frequently found.
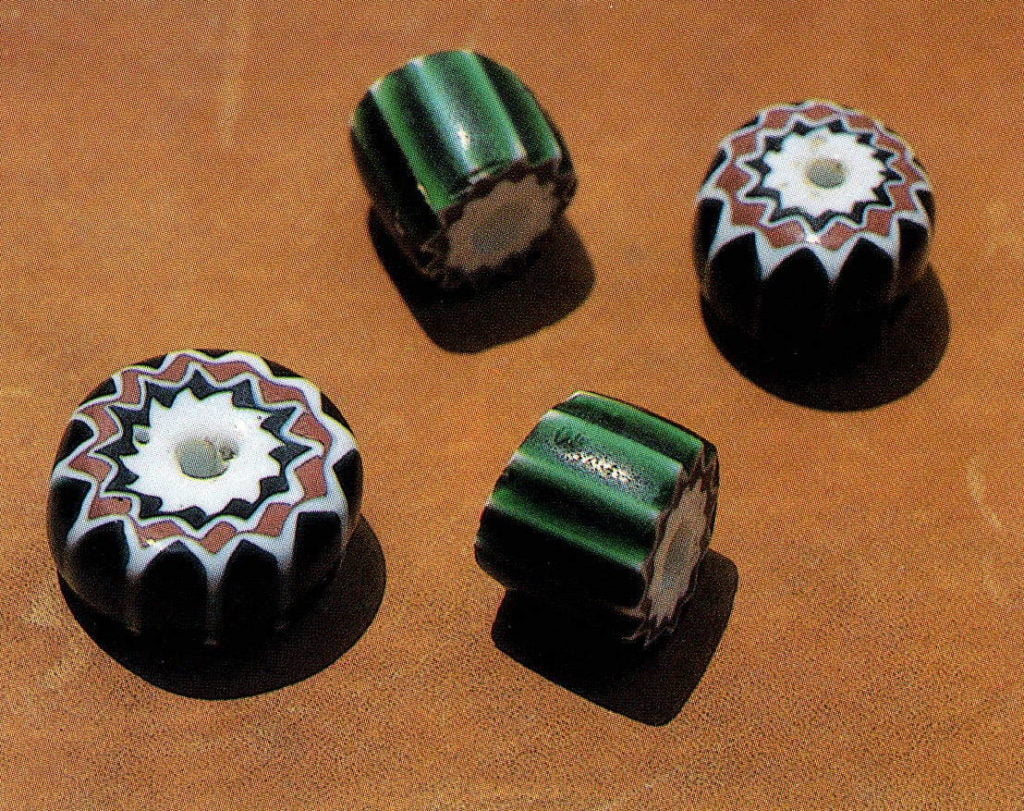
In the early 1500’s, the demand for glass beads continued to increase. The Venetians realized that in order to keep up with demand, it was necessary to send some of their drawn tubes out of the country to be made into smaller, individual beads. Because of the large number of workers available in Bohemia (now part of Czechoslovakia), the majority of the tubes were sent there. The finished beads were returned to Venice for shipment.
Other European countries soon broke into the bead industry as workers and their techniques were recruited from the Venetian guilds. The countries of Holland, France, England and Sweden are believed to have entered into this industry in the 1600’s.
In the early 1700’s, the Bohemians came into their own in the bead industry. Although they had been making glass since the twelfth century, most of their items were in the form of glassware, vases, cups, etc. Bohemia sent men to the Island of Murano to learn the craft of making glass beads. Due to the knowledge and the Venetian workers these men brought back with them, Bohemia was soon a major producer of the much sought-after glass bead.
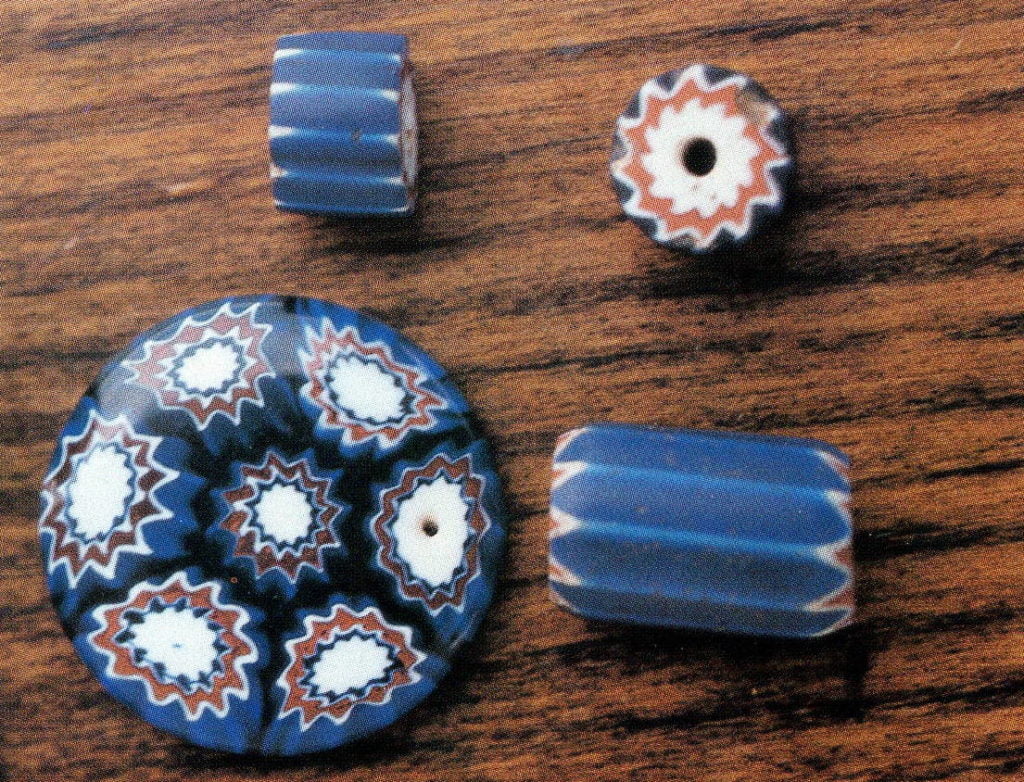
Bohemia had an abundance of the three main items needed to be successful in the bead industry: Quartz, which is used as the silican base of glass; labor willing to work the hot furnaces; and plenty of wood to fire the furnaces. Potash, an ingredient needed in glass making, does not have to be mined when it is available as a by-product of wood burned in these furnaces. Around 1866, Bohemia actually out-produced the Venetians in making glass beads.
Here at St Stephens Indian Mission, the people who are involved in beadwork state that the “Czech” are still the most desirable beads used today.
St. Stephens Indian Mission Foundation is a non-profit organization, incorporated under the laws of the State of Wyoming on March 31, 1974, and listed on page 160 of THE 1986 OFFICIAL CATHOLIC DIRECTORY. The sole purpose of the foundation is “to extend financial support to St. Stephens Indian Mission and its various religious, charitable and educational programs and other services conducted primarily for the benefit of the Northern Arapaho and Eastern Shoshone Tribes on the Wind River Indian Reservation.
